レーザーマーキングラベル開発プロジェクト
お客様から求められる新しい価値は、現状の枠組みを超えることから生まれていくものです。
ニーズにお応えする製品開発をはじめ、生産技術の向上による生産性の強化や生産ラインの立ち上げなど、
日本カーバイド工業の技術力、そして、人材力を物語るプロジェクトストーリーをご紹介します。
試作に試作を重ねて製品化。求められたのは高難度の“ロゴ入り”
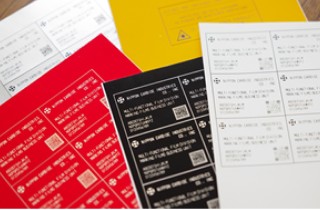
自動車の個々の車両を識別するために表示するシリアルナンバー・車輌識別番号(Vehicle Identification Number略してVIN)。主に盗難車や欠陥車、事故車などを調べる際に利用され、このVINを表示する専用ラベルとして使われているのが「レーザーマーキングラベル」です。
「よりセキュリティ性(改竄防止性、偽造防止性)を高めるために、表面にロゴを入れてほしい」という要望をお客様よりいただいたことから実現に踏み出した、ロゴ入りレーザーマーキングラベル開発のプロジェクトストーリーをご紹介します。
「よりセキュリティ性(改竄防止性、偽造防止性)を高めるために、表面にロゴを入れてほしい」という要望をお客様よりいただいたことから実現に踏み出した、ロゴ入りレーザーマーキングラベル開発のプロジェクトストーリーをご紹介します。
Member Profile
-
HAYASHI
TOMOHIRO林 智博
プロジェクト当時:
研究開発センター
フィルムグループ
グループリーダー -
SHIOMI
KYOUKO塩見 恭子
プロジェクト当時:
研究開発センター
フィルムグループ
兼 知的財産部 -
KUDOU
SHUNPEI工藤 俊平
プロジェクト当時:
研究開発センター
フィルムグループ
文字が消えず剥がせない、技術のフィルム
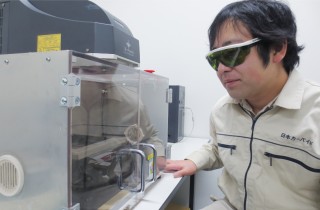
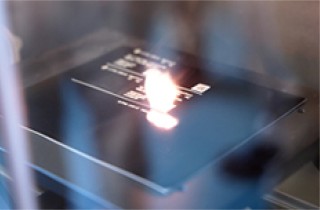
レーザービームでフィルムの一層目を削り、文字を描いていきます。
レーザーマーキングラベル『ハイエスカルAXシリーズ』とは、自動車などの車輌識別番号のほか、建設機械の製造番号表示、製品銘板などに使用する改ざん防止機能を持ったラベル用の製品です。異なる色のフィルムを積層させた構造になっており、レーザービームで表層を削り、下層を視認させることで情報(文字やイラスト、二次元コードなど)を表示します。
特徴は、インクを使用しないため、印字された情報を半永久的に表示し続けることができること。
また、剥がそうとするとフィルムが割れて、改竄や偽造などの不正改造を防止し、貼付後には、熱帯など厳しい環境下でも優れた耐久性を発揮します。
特徴は、インクを使用しないため、印字された情報を半永久的に表示し続けることができること。
また、剥がそうとするとフィルムが割れて、改竄や偽造などの不正改造を防止し、貼付後には、熱帯など厳しい環境下でも優れた耐久性を発揮します。
「その場で印字したい」ニーズを叶える“複層式”へ
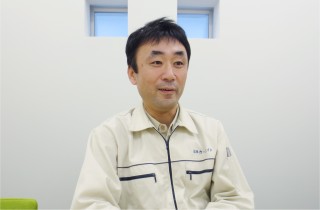
日本カーバイド工業では、30年以上前から“単層”で上から印刷するタイプのフィルムはありましたが、文字などの印刷工程を別工場で行うため、どうしてもタイムラグが生じてしまうことに。当時のお客様から「その場で印字できて確認できる方法はないか」という要望をいただき、自社のレーザー加工による印字のノウハウを活かした製品化の作業が進められました。
そんな改良を重ねた現在の“複層式”のレーザーマーキングラベルは、車の生産ラインの横でもフィルムを加工でき、その場で一枚一枚ラベルを作成しながら、さらにその場での確認も可能に。貼り直しを見込んだ印刷の外注を必要としないジャストインタイムを実現し、市場での支持を高めることができました。お客様のニーズに応え続けることで、新たな技術を生み出していく。その姿勢は今もなお、受け継がれています。
そんな改良を重ねた現在の“複層式”のレーザーマーキングラベルは、車の生産ラインの横でもフィルムを加工でき、その場で一枚一枚ラベルを作成しながら、さらにその場での確認も可能に。貼り直しを見込んだ印刷の外注を必要としないジャストインタイムを実現し、市場での支持を高めることができました。お客様のニーズに応え続けることで、新たな技術を生み出していく。その姿勢は今もなお、受け継がれています。
フィルムの剥離力バランスが難しい課題に
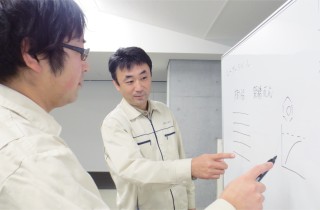
「よりセキュリティ性を高めるために、表面にロゴを入れてほしい」。そんなお客様のご要望からはじまったロゴ入りレーザーマーキングラベルの開発は、量産化へと進める段階で工藤俊平が担当を務めました。
工藤は、研究開発センター フィルムグループ(プロジェクト当時)に新人として配属。新人研修後すぐ、本プロジェクトの主担当である先輩の下でOJT研修を受けます。数ヶ月が経って、工藤は「2~3年かけて自分が担当する範囲を広げていき、できるだけ早く一人前の研究者になりたい」と思っていた矢先、先輩が退職することに。入社2年目にして先輩から担当を引き継ぎ、開発現場の最前線に立つことになりました。
「ロゴを印刷した塗工基材にフィルムを製膜後、塗工基材を剥離することで、ロゴをフィルムの中に埋め込む」という処方でお客様の承認をいただいていましたが、その時、開発現場では『塗工基材とフィルムの剥離バランス』が大きな課題に。
塗工基材とフィルムの剥離力は絶妙なバランスが求められ、剥離力が小さ過ぎると製膜時にフィルムが剥がれてしまい、剥離力が大き過ぎると塗工基材からフィルムを剥離することができない……。そんな難しい課題に、工藤は正面から取り込んでいきます。
工藤は、研究開発センター フィルムグループ(プロジェクト当時)に新人として配属。新人研修後すぐ、本プロジェクトの主担当である先輩の下でOJT研修を受けます。数ヶ月が経って、工藤は「2~3年かけて自分が担当する範囲を広げていき、できるだけ早く一人前の研究者になりたい」と思っていた矢先、先輩が退職することに。入社2年目にして先輩から担当を引き継ぎ、開発現場の最前線に立つことになりました。
「ロゴを印刷した塗工基材にフィルムを製膜後、塗工基材を剥離することで、ロゴをフィルムの中に埋め込む」という処方でお客様の承認をいただいていましたが、その時、開発現場では『塗工基材とフィルムの剥離バランス』が大きな課題に。
塗工基材とフィルムの剥離力は絶妙なバランスが求められ、剥離力が小さ過ぎると製膜時にフィルムが剥がれてしまい、剥離力が大き過ぎると塗工基材からフィルムを剥離することができない……。そんな難しい課題に、工藤は正面から取り込んでいきます。
チームが一丸となり支えた量産化
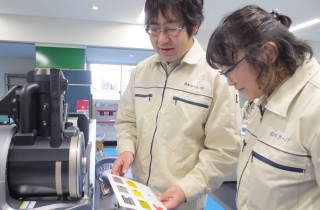
工藤が考えたのは、3つの方法でした。フィルムの原材料を変えること、製造条件を変えること、そして、塗工基材を変えること。しかし、すでにお客様から原材料と製造条件に関する承認をもらっていたため、変えられるのは塗工基材だけでした。そこで、塗工基材メーカーと協力して検討を進めていくことに。工藤はいくつもの処方や製造条件を考え、メーカーや製造現場に協力してもらいながら試作を重ねました。
先輩の塩見恭子は「通常、試作の準備から立会いまでは2~3日かかるもの。何度も試作しておりかなり労力を割いたと思いますが、工藤君の頑張りは目を見張るものがあった」と言います。
数ヶ月間の試行錯誤の末、ようやく安定して製造できる塗工基材を選定。
上司であった林智博から引き継ぎの話を聞いたときのことを、工藤はこう振り返ります。「あのときは耳を疑いましたね。不安しかありませんでしたが、チームの皆さんから『大丈夫だ!』という力強い言葉をかけていただきました」。一方、林は言います。「チーム皆でフォローしますし、大丈夫だと思っていました。なにより、彼ならできるという期待がありました」。
先輩の塩見恭子は「通常、試作の準備から立会いまでは2~3日かかるもの。何度も試作しておりかなり労力を割いたと思いますが、工藤君の頑張りは目を見張るものがあった」と言います。
数ヶ月間の試行錯誤の末、ようやく安定して製造できる塗工基材を選定。
上司であった林智博から引き継ぎの話を聞いたときのことを、工藤はこう振り返ります。「あのときは耳を疑いましたね。不安しかありませんでしたが、チームの皆さんから『大丈夫だ!』という力強い言葉をかけていただきました」。一方、林は言います。「チーム皆でフォローしますし、大丈夫だと思っていました。なにより、彼ならできるという期待がありました」。
さらなる課題へ、これからも
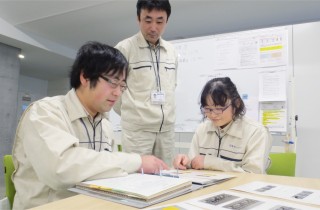
ロゴ入りレーザーマーキングラベルは無事、量産化。しかしその後も、工藤たちチームは「まだやるべきことは沢山ある」と気を引き締めます。例えば、レーザーマーキングラベルの表面が摩耗により削れてしまうとQRコードの読み取りが困難になることがあり、摩耗の激しい環境下でも使用できるよう耐摩耗性の向上が望まれていること。一方でセキュリティ性の観点より脆さも求められるため、これらを両立することが新たな課題となっていました。お客様のどんなニーズにも応えることができる、さらに高品質なものを―。新たな課題へのチームの挑戦は、これからも続いていきます。
※記事内容は取材当時のものです
※記事内容は取材当時のものです